Building a handcrafted violin is an interesting and ambitious project. Many violinists and luthiers appreciate the beauty of stringed instruments, especially the smallest of the family: the violin. Each violin has a distinct sound, which varies according to the properties of the wood and the style of the lutatio. Hearing the sound of the instrument that you have built yourself can be a particularly exciting experience. The following is a simple guide that outlines the process of building a violin. If you decide to embark on this venture, keep reading, but also buy some books on the subject.
Steps
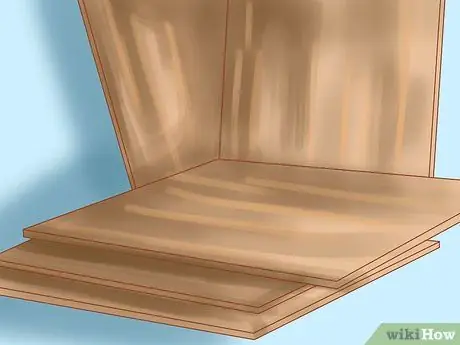
Step 1. Get the right wood
A violin is constructed primarily of maple and spruce. The back panel, sides and neck are made of maple. The front panel is typically made of spruce.
- You will therefore need to get yourself a maple board for the back, a maple block for the neck, various strips of maple trim for the sides, and a spruce board for the front panel.
- You will also need to get yourself a "shape" and some smaller spruce blocks. The shape is a block of wood with the same curves as the violin, around which to fold the maple boards to create the sides of the violin.
- The smaller spruce blocks are glued into the corners of the violin to hold the sides together and ensure stability.
- To get these ready-made materials, try lutherie websites like [1] (UK only), or [www.ebay.com Ebay] anywhere.
- Use Google to search for materials.

Step 2. Prepare the wooden planks
These must be sawed in the center, to obtain half-thick pieces. After that, they need to be glued together at the ends to form a wooden plate from which to make the back and front panels. See [www.violins.demon.co.uk/making/frontplates.htm] for more details.

Step 3. Start with the shape and corner blocks
Glue the small spruce blocks to the block-shaped orifices on the edge of the shape. Use a file or chisel to hollow out the blocks so that they follow the curves of the violin, and form the angles and shape of the violin. If you have not understood correctly, look here: [2]

Step 4. Start by folding the spruce siding to form the sides
You can use an iron or a professional iron (very expensive, but guarantees better results).
-
You will need 6 different folded parts, each for each space between the blocks - top left, top right, center left, center right, bottom left and bottom right.
Build a Violin Step 4Bullet1 - If you are using an iron, you can use old pens or some wood and rubber bands to hold each strip in place while you iron the wood around it. It will take a bit 'of time.
- Pay attention to the central parts, these need to be folded before being put on the shape.
- Once this is done, glue each strip to the block at each end, and finish the corners so that everything is smooth, neat and tidy. DO NOT glue any part on the shape, the shape will be removed later.
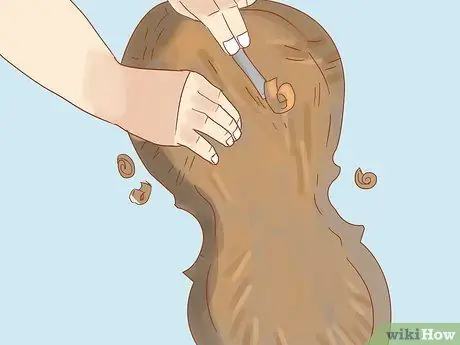
Step 5. Begin by hollowing out the front and back panels
This will likely be the most time-consuming step.
- Start by using some templates (you can trace the contours of another violin or search for patterns, shapes and measurements online) and saw along the contour you traced to get the template. There is no need to be too precise.
- To finish the shape, you can chisel or sandblast the wood. At this point, you need to give the right shape and curvature. The bottom of each panel must always remain perfectly flat and the perimeter must always have the same thickness (about 0.5 cm).
-
Use the shape as a guide to carve or chisel the corners of the right thickness, and at this point work on the outside of the panel to achieve a refined curvature. The inside of each panel should be chiseled and follow the contours of the outside.
To do this first, you could use a drill
- This operation must be repeated for both panels. Front and rear.
-
Cut the f-holes with a drill and a hacksaw on the front panel - use a diaphragm for this process. The most experienced luthiers also smooth the corners of all panels. You will also need to mount the so-called “bass barr” on the center panel - a wooden bar glued to one side that follows the line of the lowest string. This component amplifies the low frequencies.
Build a Violin Step 6 Step 6. Carve the handle
Use diaphragms to complete this process. Wrong neck length could have disastrous effects on intonation. Sand and finish the handle perfectly. You can use a drill to help you make holes in the headstock. Make sure the handle is smooth and sandblasted.
Build a Violin Step 7 Step 7. Detach the blocks and panels from the shape with a chisel or flat screwdriver
Plan or chisel the inside of each block to create a smooth curve aligned with the rest of the side of the violin. Use the iron again to fold some small pieces of maple paste, and glue them to the top and bottom of the sides, inside the violin. These serve to provide structural support.
Build a Violin Step 8 Step 8. Glue the top panel to the sides
Cut a small section (which has the same shape as the end of the handle) from the side block and the front panel, to create the recess in which to fit the handle. Continue until the angle of the handle is correct.
Build a Violin Step 9 Step 9. Glue the back panel
Build a Violin Step 10 Step 10. Assemble the other components
You will need to assemble the bridge, fingerboard, strings, and tuning pegs. Of course, you will also need to get a bow to play.